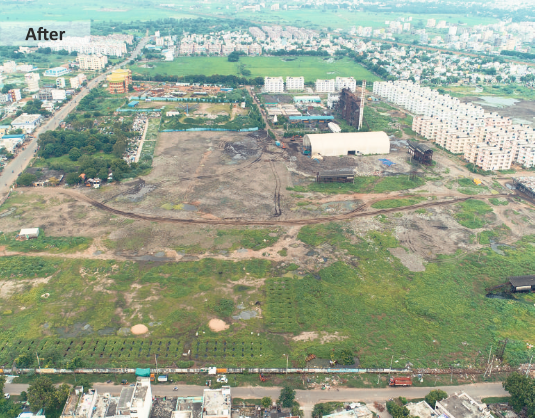
Ajithsingh Nagar Dumpyard Reclamation Project, post-completion image provided by Zigma
Erode-based Zigma Environ Solutions Pvt Ltd is one of India’s first and largest integrated landfill mining companies. Established in March 2015 by B Dharmaraj, Ku. Tha Ilangovan, K. P Mutharasu and Nagesh Prabhu. C, Zigma currently operates 12 plants across five states in India, processing approximately 10,000-12,000 Tons Per Day of legacy waste. SolidWasteIndia’s Aafrin Kidwai caught up with the inspiring Mr Prabhu soon after the completion of the high-profile Ajithsinghnagar dump yard reclamation project in Vijayawada.
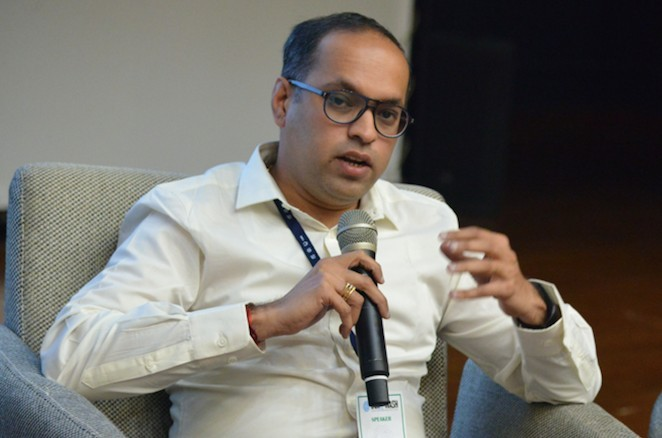
Q1. You set up Zigma in 2015 with no experience in the waste sector. Could you share with us your journey into landfill mining?
We are a group of serial entrepreneurs from diverse fields who, in 2015, were the first to introduce landfill mining in India in the form of an integrated model. That is, the ULB hands over a dumpsite to us and we return it to them as reclaimed land. This is unlike other companies that earlier provided such services but on a piecemeal basis. We also introduced the concept of ‘Payment Against Performance’ so that ULBs pay us each month when we show progress. This is also a win-win situation for the ULB’s who do not have to buy expensive machines which eventually turn out to be white elephants for them with no post-project application.
We work on a zero-residue principle and are committed to the responsible disposal of aggregates. “Responsible” means, for instance, that if a lot of fine soil is generated, the soil before disposal is checked for leachability, organic content and salinity. This will ensure that the pollution created within the dumpsite is not transferred off-site.
Q2. Zigma has shown phenomenal growth in the last five years…
Scalability is essential for a bio-mining company. Five years ago, each of our plant processed between 100 to 250 TPD. Today, we have scaled it up to 1000 TPD. We currently process more than 10,000 TPD legacy waste from our plants. Till the last FY we had processed 2 million tonnes of legacy waste and this year alone we intend to cross 2.5 million tonnes. We have reclaimed more than 100 acres of land so far and responsibly disposed more than 1.5 lakh tones of RDF and employ more than 600 people (directly and indirectly). The idea is to get the country rid of landfills.
Q3. The CPCB recommends bio-mining as a preferred option to clear dumpsites. In your experience, how enthusiastic are ULBs themselves in getting the dumpsites cleared, considering the costs involved?
Each ULB has a different goal for clearing a dumpsite but they face certain challenges. On the one hand, they have to build infrastructure to handle their fresh waste but at the same time, they don’t have any land to setup the same. And when they intend to acquire new land for this purpose, there is often agitation from the people owing to the NIBY syndrome. Clearing dumpsites using bio-mining resolves their problems quickly and permanently. That is why there is huge enthusiasm among the ULB’s recently for bio-mining. The key is to carry it out scientifically and in a responsible manner.
Q4. What are some of the biggest challenges you face while dealing with ULBs?
Integrated landfill mining is a relatively new concept and a lot of ULBs are still trying to understand our methodology. We spend a lot of time explaining them about it at various forums and interactive sessions.
ULBs must realize the dumpsites that we clear in a short span of a few months have been formed over many years. Bio-mining is not merely segregation, nor is it like a manufacturing process where you maximize output by simply installing more machines. Rather, it is a long-drawn process impacted by the macro (eg: weather) and microenvironment (eg: pandemic). Of course, it is scalable, but there are inherent limitations.
Also, it is unreasonable to expect us to invest in world-class infrastructure with closed sheds, concrete floors, etc since we are at the site for a short period. We have to ensure that our machines are mobile and modular so that at the end of the contract, we take them back. Explaining these things to ULBs is not easy.

Q5. So far, Zigma has treated – or is in the process of treating – dumpsites ranging from 2 – 49 acres. How different is each dumpsite experience?
The fact is, whether the project is big or small, we need a minimum set of equipment for each site since it impacts the quality of aggregates, which in turn impacts whether we will be able to dispose it responsibly. It has to be understood that just trommels wouldn’t help as they just segregate certain fractions based on size without concentrating on the applicability of the aggregate’s disposal. We have a separate R&D team working on smaller projects but are increasingly finding the latter unviable since certain machinery cannot be made modular. Their efficiency decreases and the quality of aggregates is hampered. Hence, Zigma is currently concentrating on large projects only. But we understand that smaller projects are many and are very important to be reclaimed for the overall well-being of the society. Hence we are working on a sustainable and environmentally friendly solution for smaller projects as well.
Q6. What are some of the challenges associated with bio-mining active landfills?
Most of the dumpsites we treat are active dumpsites, which is challenging. Treating legacy waste is very different from treating active waste, which we try explaining to the ULBs. We are unable to clear fresh waste (less than six months old) due to the organic waste component. We need to stabilize and degrade organics in order to process them further and therefore bifurcate the old and fresh waste during our operations.
The pre-stabilization process is of critical importance since it ensures that active organics are degraded by the bacteria and stabilise them where they are safe for segregation. Most of the tenders issued by ULBs don’t take the pre-stabilization process seriously since they probably do not know the importance of this concept. But we consider this as one of the most and integral part of the bio-mining process without which it is a highly unsustainable model for the environment.
Q7. Where do you acquire your machines from?
We have a technical association with a South Korean company which is a landfill mining major. They have experience in mining over one hundred dump sites across the globe and are in the industry since more than two decades. At the same time, we have a very strong in-house research team from various industries. We design, fabricate, assemble and commission all our machines ourselves and hence are completely “atmanirbhar”. Our team uses a combination of different machines and customises them based on the waste characteristics. We have 12 international patents for the biomining machines and they are designed exclusively for biomining applications. Our machines are rugged and are apt for handling legacy waste with both, precision and scale.
Q8. Each biomining project has its own unique set of issues. How do you determine what machines are deployed for each project?
All our machines are flawlessly built to ensure that waste is segregated efficiently so that the output can be repurposed. Having said that, we have a standard set of machines but do a lot of customization based on R&D. We also do a pre-assessment and waste characterization study at every new site.
The pre-stabilization process is the most important step in landfill mining, followed by processing, segregation, and responsible disposal of aggregates. The waste at the dumpsites is a heterogeneous mixture dumped haphazardly. It hasn’t received oxygen to get itself degraded. Hence, the first thing we do is make the waste ready for processing and segregation by stabilising the same.
Based on this, we make a final determination of our machines. For instance, if there are more plastics, we use a lot of blowers, including suction blowers, and so on.
Simple changes lead to efficient segregation which results in aggregates of such fine quality that nobody can complain. Today, we supply to more than 23 cement plants in India because our quality is assured.

Q9. Typically, how much revenue are you able to generate from the disposal of aggregates?
The costs associated with the disposal of aggregates differ from place to place. The recyclables are less than 2%. You are essentially left with RDF, maybe iron scrap, 0.5% of glass, maybe one percent of plastics which are very difficult to segregate and have to be done manually. These are sold to State Pollution Control Board registered recyclers.
Regarding RDF, the MoHUA RDF guidelines specify the cost incurred in disposing the same. Since we do not have the liberty to choose which dumpsite we are reclaiming, the cost of RDF inherently depends on how far the cement companies are from the dumpsites and whether such cement factories have the infrastructure to use RDF as alternate fuel. Hence, our balance sheets say we are not making any money out of RDFs – it’s actually an expense since very few of our plants are close to cement companies. All this is a value-added service we give to the ULBs since they don’t have the wherewithal to do it themselves.
The disposal of soil, stones and rubbles are also not a money-making exercise as it requires us to spend on transportation to the desired location, which is also expensive.
Since reclamation of land in the fastest possible time is the target that we work on, we work on a highly scalable and environmentally responsible applications always.
Q10. Bio-mining and bioremediation are not economically viable, a fact endorsed by the CPCB. Where are you earning your wealth from?
(Laughs) We tell everybody there is no wealth in waste. In India, the waste that reaches dumpsites has been scavenged at multiple levels and there’s nothing of any value left in it. We don’t make profits from the disposal of aggregates. Our margins are well-covered within the processing costs specified by the CPCB, ie. Rs 400-700 per cubic meter. It must be understood that public health is not available free of cost. It costs to clear these dumpsites and being cheap is not always sustainable.
Q11. The CPCB has provided elaborate Guidelines for Disposal of Legacy Waste. What further steps can be taken to facilitate biomining and bioremediation of dumpsites in India?
Unfortunately, unethical practices are rampant in the market. Many contractors dump aggregates that are expensive to dispose of, into SLFs as there is no proper vigilance. There should be watertight tenders outlining the methodology to be followed, with due emphasis on pre-stabilization and zero rejects. The states of Tamil Nadu and Andhra Pradesh are front-runners in this area. There is no points in excavating 100% legacy waste but disposing only 70% to 80%. Only when a zero reject policy is adopted the contractors will adopt the best practises and truly a circular economy shall be established. Repurposing the aggregates which today lie in these dumpsites as an eyesore, must be the mantra for the way forward.
Better monitoring by concerned authorities like the NGT and SPCB is also desirable since CPCB rules and SWM Rules are being flouted. For instance, there no leachate management, aggregates are not disposed of responsibly, RDF is not being sent to cement plant but sent to local bhattis, jaggery making industries which burn below 90 degrees, risking release of harmful gases into the environment.
The single-trommel model also needs to be abolished since the RDF, inert or other aggregates generated from this cannot be of disposal quality. They are simply shifting the dumpsites problem to some other place, which can ultimately cause an environmental fiasco in the long run and proves disastrous. It is not a sustainable model. ULB’s tend to choose them as they feel it is cheap.

Credentials of the contractors must be given paramount importance while calling for the tenders and the contractor’s capability to dispose the aggregates must also be assessed along with their past experiences. There is need to understand that bio-mining is not just segregation using trommels but it is much more than that. There is a difference in methodologies to be adopted when you carry out this activity in Rajasthan versus in Kashmir.
Having said this, we would like to appreciate the efforts taken by the Swacch Bharath Mission, the Ministry, Central and State Pollution Control Boards in trying to bring in lot of information regarding the right way to carry out bio-mining and various standard practises to be followed.
At Zigma, values like sustainability, circular economy, scientific methodology, and environmental well-being are above all else. We request the CPCB to go one step ahead and give us the exact framework on the tests, documentation, responsible disposal of aggregates etc. only then will we able to realize the goal of zero waste rejects.